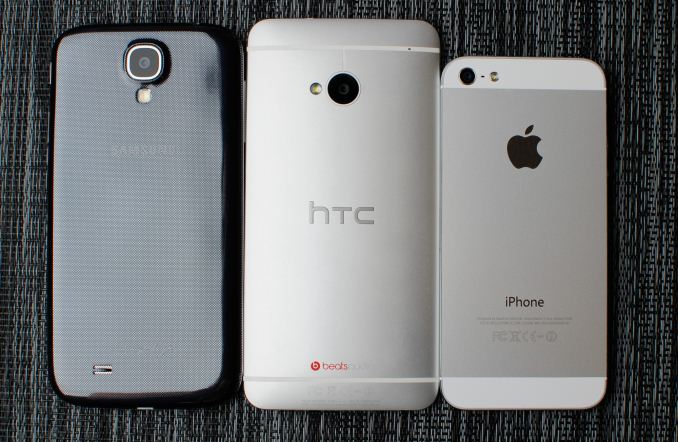
Within the past four years, the smartphone market has changed drastically. Displays have dramatically increased in quality. Battery life has increased. As OEMs converge on largely similar platforms, the material design of a phone has become increasingly important. Almost every OEM has had a major shift in the material design of their devices as the market becomes increasingly saturated and competitive. This is especially true at the high end where the upgrade cycle has become lengthened. As people find less and less reason to upgrade to the latest and greatest, OEMs have to change things to stave off decreasing growth. Overall, this seems to mean going “back to basics” with their new devices, which often entails improved material design.
This seems to make very little sense, especially when there are a great deal of people that simply aren’t concerned with materials. It’s not unusual to hear the argument that because everyone uses a case, the design of the device shouldn’t matter. It’s often said that aluminum devices are less durable, heavier, and with worse radio reception than one made of polycarbonate. Other issues often cited include uncomfortable skin temperatures under load. Higher cost is also a problem, one that OEMs will often cite internally. With glass, it’s almost universally understood that any drop risks shattering the brittle back. So the question remains: Why is it that OEMs continue to push material design?
Without a doubt, this is a complex topic. Material choices entail a huge number of trade-offs. There isn’t any one material that has the best compromises either. For the most part, there are three key materials that smartphones are made from. These three materials are plastic, glass, and metal.
Plastic
Within plastics, the most commonly used material is polycarbonate, which has high impact resistance, relatively good temperature resistance, and it’s also extremely flexible. A great example of polycarbonate would be the battery door of the Galaxy S and Note line, or Nokia’s Lumia devices. In general, it’s almost impossible to point to a phone with a polycarbonate external build that has reception issues, as polycarbonate effectively doesn’t attenuate radio signals, as shown on page 38 of this study of radio propagation differences. As the market becomes squeezed by decreasing profit margins, the low price of polycarbonate relative to glass or metal is also a significant advantage that can’t be overlooked.
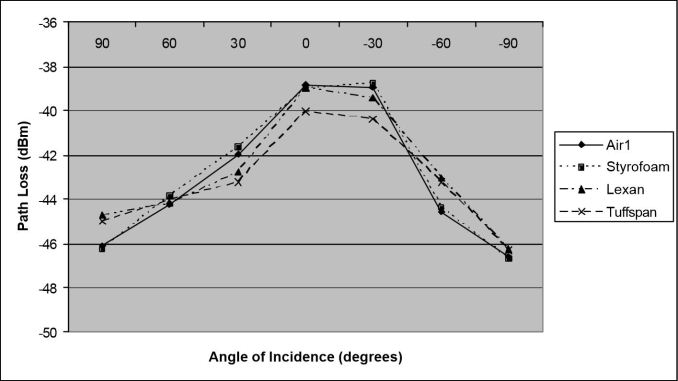
While these are advantages are reason enough to make a smartphone or tablet with a polycarbonate casing, there are disadvantages as well. Polycarbonate is a poor conductor of heat, which means that with today’s thermally constrained devices, true nominal clockspeed for both CPU and GPU on the SoC will be lower than a phone or tablet that is made of metal such as aluminum and magnesium. The same is also true when comparing a device made with polycarbonate and one with glass in general. For reference, the thermal conductivity of aluminum is 205 watts per meter kelvin, 156 W/m*K for magnesium, .8 W/m*K for ordinary glass, and .22 W/m*K for polycarbonate. The unit refers to the rate of energy transfer needed to heat up a length of material by a certain unit of temperature. This means that in today’s phones and tablets, one made from plastic will generally run slower in intensive games than one made of metal or glass, if all else is equal.
On top of this, while polycarbonate is extremely impact resistant, the flexibility of the material is a major issue for smartphones that have to be as thin and compact as possible. People often bring up the car analogy to argue that polycarbonate protects a phone or tablet better, but there’s no such thing as a crumple zone in a phone. Even the back cover serves a purpose, as antennas are inserted into the back cover in order to have the space for the huge number of frequencies supported. Bending the back cover into the phone is often a dangerous problem, as it will affect the delicate antenna connectors, which are often small, spring-like pieces that make contact with the back cover. This is an issue, as while the metal antenna connectors are elastic to a certain extent, once stretched too far it won’t spring back. One of the most notable examples of this issue can be seen with the Tegra 3 variant of the HTC One X. This variant of the One X would often lose all WiFi and Bluetooth reception due to crushed antenna connectors. Fixing the problem required additional reinforcement to prevent the back cover from bending in too far. As seen in the photo from iFixit’s teardown of the Galaxy S4 below, the connectors are small gold-plated nubs that touch parts of the back cover.
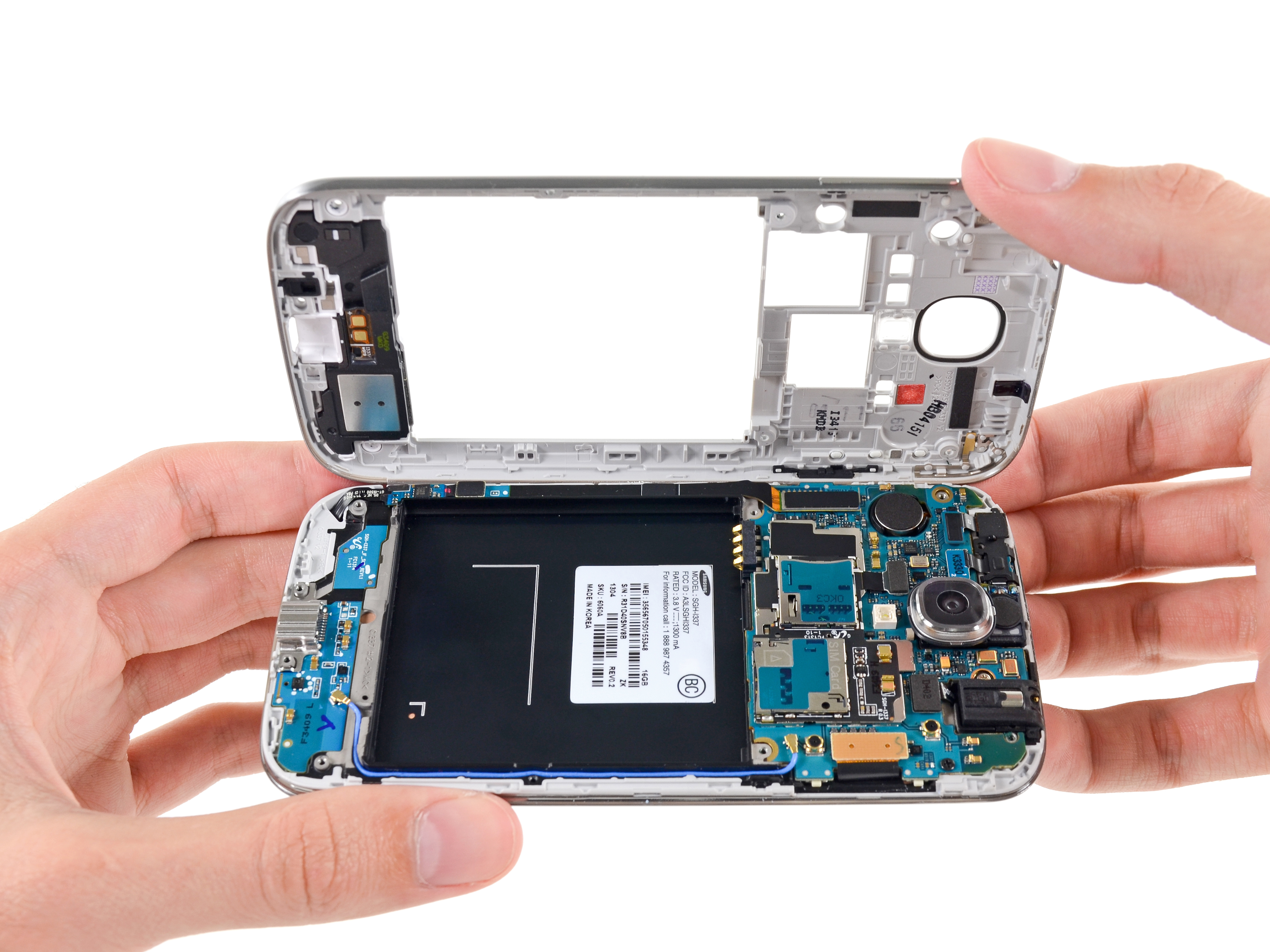
Metal
On the other end, metal is often hailed by reviewers as a superior material. However, most reviewers focus upon look and feel, rather than the technical advantages and disadvantages of using metal. Of course, metal is an extremely broad term and comprises around 80% of the known elements in existence. For this discussion, the key metal used for the outer casing is aluminum. Magnesium is another commonly-used material, but is mostly limited to the midframe.
Of course, aluminum alloys have their advantages as well. With the stiff alloys used in smartphones and tablets, there is a significant structural advantage that helps to protect internal components. To go back to the car analogy, because there aren’t crumple zones in a compact phone or tablet, there is only the safety cell. The safety cell is made to be as rigid as possible to prevent crushing the contents within the safety cell. In short, aluminum is actually more durable, not less. As pointed out back in the iPhone 4 review, the external antennas required by all-aluminum designs can give better reception and performance than internal antennas. Even today, it’s possible to see better reception performance from an all-metal device. For example, the Sprint One M8 has a higher effective isotropically radiated power (EIRP) on 1900 MHz CDMA than the Sprint Galaxy S5. Higher EIRP generally translates into better radio reception, although it also takes effective isotropic sensitivity (EIS) to see the full picture.
Because of metal’s higher stiffness, it’s also harder to scratch the surface. However, with anodization treatment, scratches are more likely be visible if they expose the untreated surface. Another key advantage is the much higher thermal conductivity of aluminum, which allows for better performance in situations where a device is thermally limited. After all, heat sinks are made of aluminum and/or copper, not polycarbonate or glass. The best example of this can be seen in the comparison between the Galaxy S5 and HTC One (M8) in the T-Rex rundown test, as the frame rate of the One (M8) is significantly higher than the Galaxy S5’s, as seen in the graph below.
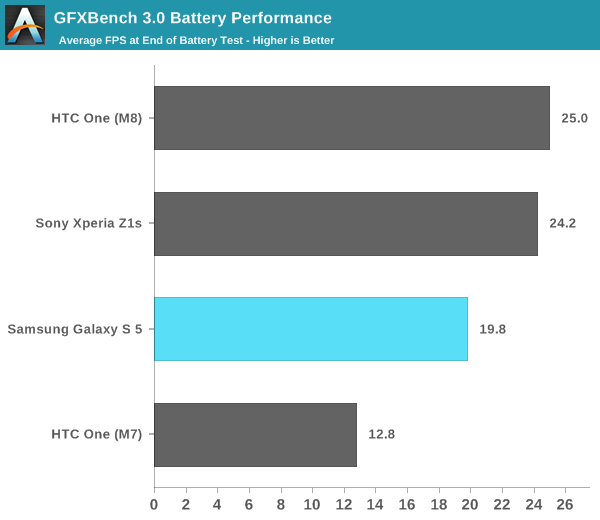
Like every other material, Aluminum is also not the perfect material to make a mobile device. As a result of making the device from metal, it’s impossible to use internal antennas unless plastic/glass “windows” are used to allow signal in and out of the phone. This means that the device will be less isotropic (direction-independent) in its reception of radio signals. Even with external antennas that turn parts of the metal casing into an antenna, detuning that occurs when a hand touches the antenna or bridges it to another conductive body is a major problem, as is the need to support multiple frequencies with an external body that isn’t necessarily able to change, as the iPhone 5s/HTC One (M8) can’t look radically different from operator to operator. While the use of multiple antennas (receive/transmit diversity) and active antenna tuners have made all-metal designs possible, there is still a noticeable difference in radio reception. Whether this difference is for better or worse depends upon the frequency used.

Outside of radio reception, aluminum alloys’ lower limit of elastic deformation means that while the casing is better at protecting internal components, it’s more likely to receive cosmetic damage. On the other hand, polycarbonate is more likely to come out of a drop without dents or gouges. Aluminum bodies are also significantly more expensive, as the time and cost associated with working the material into a final product means that the difference in price can be as great as an order of magnitude. This can take away from other aspects of the device. Finally, while aluminum is far more effective at dissipating heat than polycarbonate, this also means that the polycarbonate device will have lower perceived skin temperatures under load. What that means is that it’s more comfortable to hold a polycarbonate-bodied device even if the internals are at higher temperatures. This also means that low temperatures will cause an aluminum-bodied device to feel much colder than a polycarbonate-bodied one.
Of course, magnesium changes things up as well. It’s lighter than aluminum due to its lower density, more RF transmissive than aluminum, and in general, carries many of the advantages that aluminum does over plastics such as polycarbonate and aluminosilicate glass, which include high thermal conductivity, relatively high rigidity, and relatively better scratch resistance. In theory then, magnesium would be better than aluminum.
Unfortunately, from a mass production standpoint magnesium casings are generally infeasible, although still possible. This is primarily due to the reactive nature of magnesium in oxygenated environments, and due to outgassing that occurs during the baking process. Without surface treatment, magnesium rapidly corrodes as well. This means that it’s not currently feasible to use magnesium as an external casing, although many manufacturers use it for the midframe.
Glass
Not to be forgotten, glass is another possibility for the external casing of a tablet or smartphone. It is the most rigid of all three materials and resists scratches the best. However, it is also the most brittle and susceptible to shattering. This is because glass can only deform elastically. Aluminosilicate glass, more commonly referred to as Gorilla Glass (when made by Corning) is the most common type of glass used for the external casing of a phone. It is between aluminum and polycarbonate when it comes to thermal conductivity. However, it is only slightly more conductive than polycarbonate, and far less conductive than aluminum. It also doesn’t significantly attenuate radio signals, which means that internal antennas can be used. Of course, the disadvantage is that glass is incredibly fragile, and can pose a major safety hazard. The shape of the phone is also significantly constrained. This is why glass-bodied devices have generally been small and the glass portion of the device is generally a flat sheet.

As mentioned previously, there are plenty of complications as well once you factor in the actual layout of the device. Thermal dissipation of a polycarbonate-bodied device can be improved by using a magnesium midframe that dissipates heat into the display and other components. This increases the rate of heat transfer from internal components to the air/hand. Wall thicknesses and different types of plastic, metal, and glass can significantly decrease the severity of issues associated with the disadvantages of various materials. For example, adding ABS plastic to polycarbonate can significantly increase the rigidity of the material. Applying anti-shatter film to glass can catch shards in case the glass shatters to reduce the hazard involved in shattered glass. New antenna tuning technologies can enable all-metal devices.
Conclusion
Of course, the question still remains. Why is it that all of this matters? After all, Apple didn’t have to worry about thermal dissipation with the iPhone 4 because the SoC didn’t generate enough heat, but they used a steel side ring and glass back cover. While the glass back cover and stainless steel ring was more effective at protecting the internal components, minor improvements to drop protection and possible improvements to reception wouldn’t be strong justifications for pursuing such a design. So why would Apple do this?
The answer lies in industrial design. While it’s all too easy to conflate this with pure aesthetics, industrial design is a crucial aspect of any device. After all, smartphones and tablets are both touched all the time, and while we look at the display primarily, the shape, look, and feel all dramatically affect the experience. If it fits the hand better, feels better, and looks better, it is better. Unnecessary elements hurt the focus of the design, honest design helps it. Good design is obvious and invisible. It’s only when we use something poorly designed that we see what is well-designed. Advances in technology can and do fix the issues that materials have, but nothing can fix bad design. While most of these are subjective, as the mobile industry reaches saturation, both industrial design and material design will become crucial differentiators. If anything, it already has.